Continuum Testing
- Ronda Coryell
- Mar 9, 2013
- 3 min read
I was asked by Stuller to test the silver alloy called Continuum. It is a sterling alloy that is over 95% fine silver containing no nickle. I found this metal to be quite hard as compared to some of the other silver alloys I have tested. I tested the malleability when I was teaching a metalsmithing class two weeks ago. It was much harder to manipulate with anticlastic metalsmithing and forging it took a bit more work as compared to other silver alloys I have tried. I can understand why they say it would be good for die striking or milling products. The fact that it is harder than most of the silver alloys I have tested makes it the perfect alloy for fabricating clasps and mechanisms. It can be spot soldered like gold. It can be fused, granulated and enameled. It also did well with laser welding. Making the same clasp, Vasken soldered his while I fused mine.
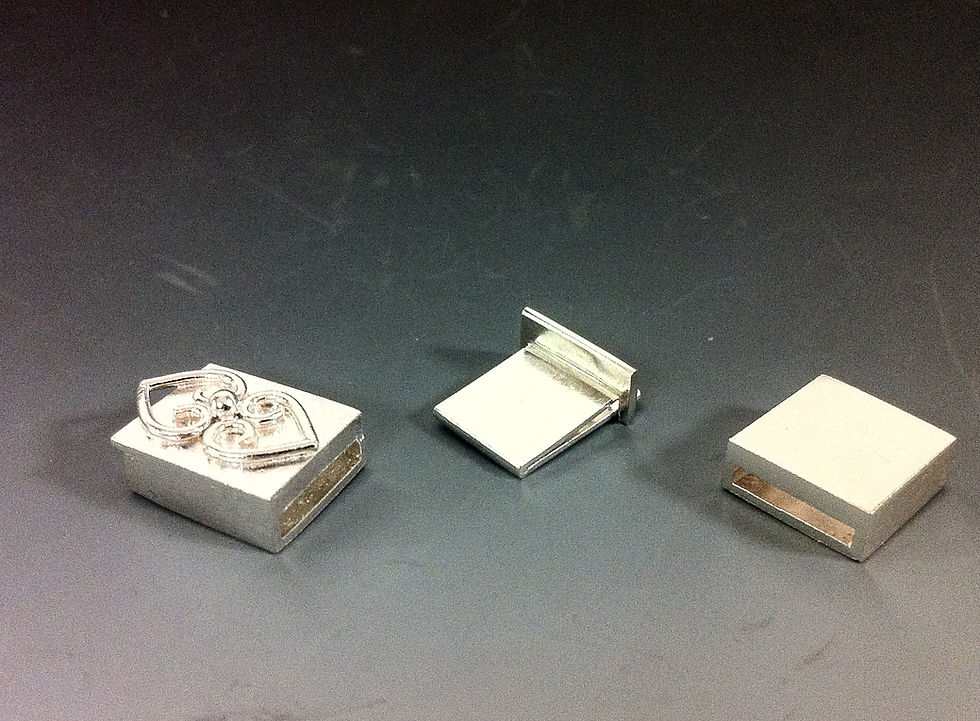
Box Clasps fabricated in Continuum
The box clasp below was soldered using hard and medium sterling solder, the decorative one, above, on the left has been fused start to finish.

Soldered using Hard & Medium Sterling Solder
Vasken fabricated his clasp using hard and medium solder. He did tests first on both an aluminum silicate block and a charcoal block.
Vasken found that the best results were to coat with boric acid/alcohol mixture and use Batterns flux for seams and solder while working on the charcoal block rather than aluminum silicate block. He loved the way it reacted to sawing because it was like working with 14k gold, firm yet easy to cut and can be spot soldered as you would with gold.

Test Samples Soldered with and without coating with Boric Acid
I fused a the same box clasp start to finish using no boric acid/alcohol except when annealing. I would coat everything in Batterns flux and fuse. The metal fused beautifully. There was no firescale. The fusability was quite good and the metal did not slump when heated to the extreme temperatures of fusing and had no firescale.

Fused Box Clasp
Vasken pointed out to me that I could now granulate on it since I had not used solder. Results were quite impressive. The wire I had extending past the clasp did not slump but was quite rigid.
I went one step further and did a bit of torch fired enameling on the fused clasp with successful results. There was bit of black on the bottom that was exposed to the flame, as I had not coated the clasp in any boric acid/alcohol mixture. The black was not a penetrating firescale and was easily removed with fine sandpaper.

Granulated Fused Box Clasp
I did not find the tarnish resistance of continuum to be quite as good as with Sterlium and the malleability was not as good as with the Sterlium. The castings are fresh from pickling. The second photo shows the pieces after 9 months of sitting on the shelf. Vasken and I find that both of these alloys are superior to traditional sterling.
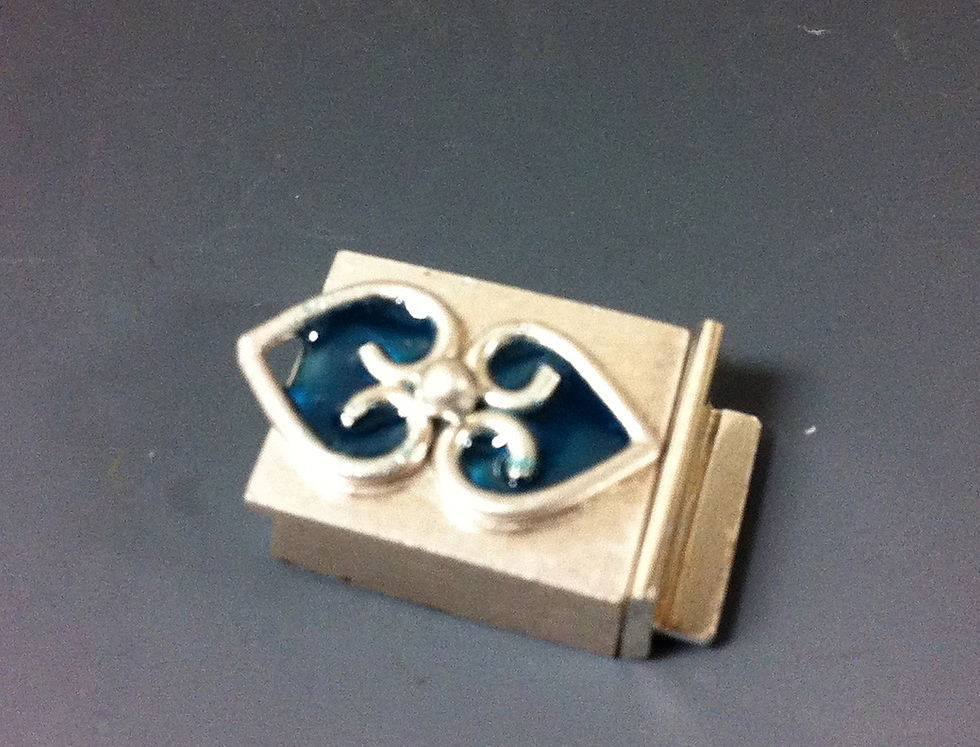
Torch Fired Box Clasp

Back after torch fired enameling. Half was sanded slightly to see if there was firescale. none

Sterlium on Left, Continuum on Right after pickling

Sterlium on Left, Continuum on Right. 9 months after casting
Kommentare